VENSOZ® D-Bio, VENSOZ® T-Bio
MADE BY BIOBASED POLYURETHANE

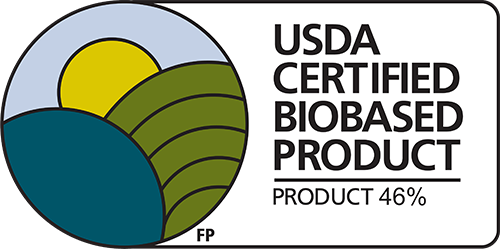
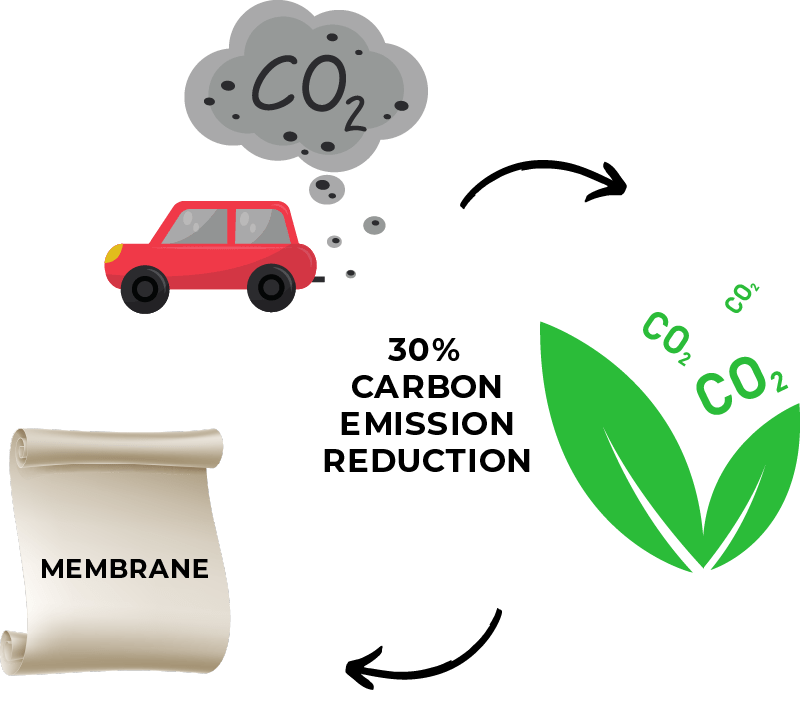
Ventex D-Bio polyurethane membrane provides a waterproof and breathable layer for fabrics and can be used in various applications.
Ventex D-Bio membrane is laminated to textiles using thermoplastic moisture-curing adhesives to provide durable and soft products for various activities.
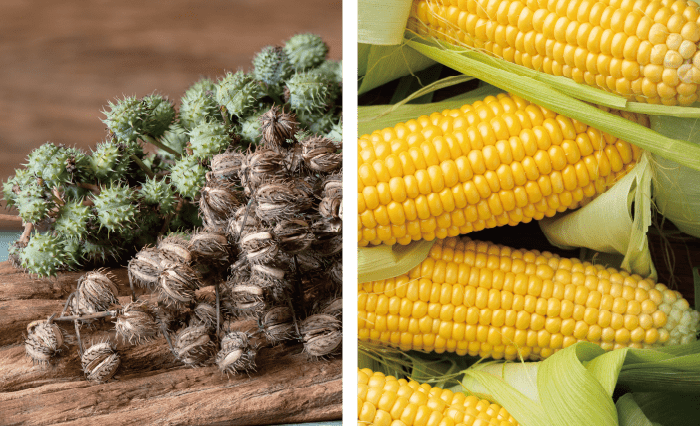
![]() |
![]() |
![]() |
![]() |
---|
Items | VENSOZ® D-Bio | VENSOZ® T-Bio |
---|---|---|
Composition | 54% Polyurethane with 46% Bio Polyurethane |
63% Polyurethane with 37% Bio Polyurethane |
Character | Hydrophilic Non-porous |
Hydrophilic Non-porous |
Standard Colors |
White/Clear | White |
Thickness [μ] |
17±2 | 17±2 |
Width [mm] |
1,520 ±15 | 1,520 ±15 |
Weight [g] |
20±3 | 20±3 |
Length/ Roll [m] |
500 | 500 |
Minimum Order |
10,000M | 10,000M |
Elongation [%] |
- | - |
✭Water proofness [mmH2O] *JIS 1092B |
>20,000 | >20,000 |
✭M.V.P [g/㎡・24hr] *JIS L 1099B-1 |
>20,000 | >40,000 |
✭M.V.P [g/㎡・24hr] *JIS L 1099A-1 |
>3,000 | >4,000 |
Certificate | USDA | USDA |
Remarks | 40% Bio material (Corn 1 : 1 Castor oil) |
37% Bio material (Corn 100%) |
※This is not the material spec but measuring data at factory for the comparison
VENSOZ®-T GRX™
Keeps your body DRY & WARM

- The membrane has passed the GRS (Global Recycling Standard) certification, and the corresponding transaction certificate (TC) file can be provided. It is a PU membrane made by post consumer waste plastics from Taiwan's electronics industry.
- The physical properties are not much different from the general PU film(M.V.P part is slightly lower).
- If it can be combined with recycled polyester face fabric, the inner lining can also go to the corresponding recycling category.
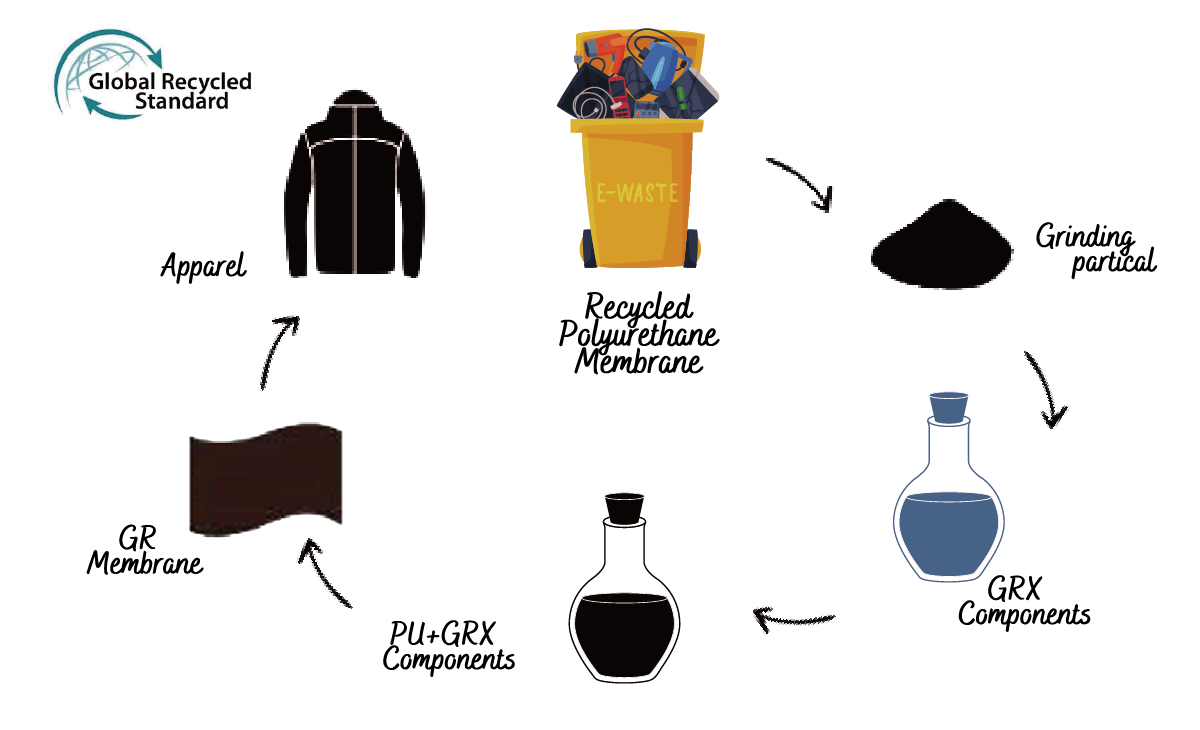
![]() |
![]() |
![]() |
![]() |
---|
Items | VENSOZ®-T GRX |
---|---|
Composition | Polyurethane with 27% recycled material |
Character | Hydrophilic Non-porous |
Standard Colors |
White |
Thickness [μ] |
18±2 |
Width [mm] |
1,520 ±15 |
Weight [g] |
- |
Length/ Roll [m] |
800 - 1000 |
Minimum Order |
20,000M |
Elongation [%] |
200 MD; 200 CD |
✭Water proofness [mmH2O] *JIS 1092B |
>15,000 |
✭M.V.P [g/㎡・24hr] *JIS L 1099B-1 |
>70,000 |
✭M.V.P [g/㎡・24hr] *JIS L 1099A-1 |
- |
Certificate | GRS |
Remarks | 27% recycled material is form waste plastic particles of the electromics industry in Tiwan |
※This is not the material spec but measuring data at factory for the comparison
VENSOZ®-T Zero
Keeps your body DRY & WARM

- BLUEsign and ZDHC claim to reduce use of the hard solvents, mainly DMF, as they may cause health and environmental effects.
- We have developed a new, highly functional membrane which uses soft solvents.
- It is a revolutionary development for making high functional PU, so that the TPU membrane which is solventless cannot provide high spec functional value as below.
![]() |
![]() |
![]() |
![]() |
---|
Items | VENSOZ®-T Zero |
---|---|
Composition | 100% Polyurethane |
Character | Hydrophilic Non-porous |
Standard Colors |
Clear/White |
Thickness [μ] |
16±2 |
Width [mm] |
1,520±15 |
Weight [g] |
18±2 |
Length/ Roll [m] |
800 - 1000 |
Minimum Order |
20,000m |
Elongation [%] |
- |
✭Water proofness [mmH2O] *JIS 1092B |
>15,000 |
✭M.V.P [g/㎡・24hr] *JIS L 1099B-1 |
>50,000 |
✭M.V.P [g/㎡・24hr] *JIS L 1099A-1 |
- |
Certificate | - |
Remarks | Non solvent |
※This is not the material spec but measuring data at factory for the comparison
VENSOZ®-TPU Bio23 LM, VENSOZ®-TPU Bio13 HM
Keeps your body DRY & WARM

BIO TPU uses DuPont's biomass technology. TPU is made by adding raw biomass materials. Compared to the petroleum refining process, refining raw materials through plant fermentation can reduce both energy consumption and greenhouse gas emissions by 40%.
We obtained the biological quality certification (Certificate No. B 13-166-A) in 2013. We use biological materials to be earth-friendly and follow environmental protection guidelines. Products are available in 21% and 13%.
Do you need green products? We also provide bio products.
Like general TPU products, it maintains its softness and excellent water resistance. It also has bio ingredients. Products are available in 23% and 13%.
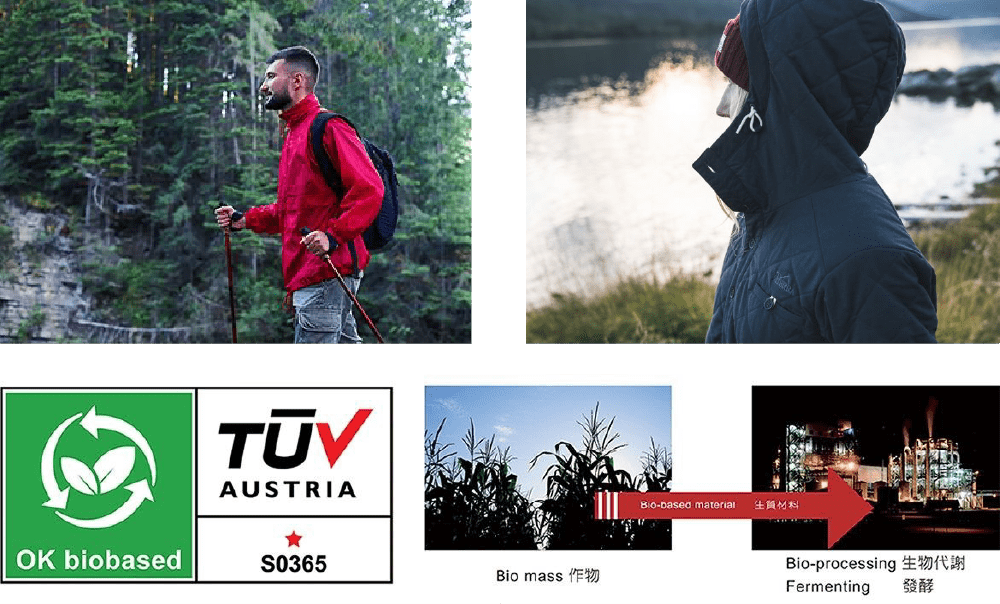
![]() |
![]() |
![]() |
![]() |
---|
Items | VENSOZ®-TPU Bio23 LM | VENSOZ®-TPU Bio13 HM |
---|---|---|
Composition | Thermoplastic Polyurethane with 21% Bio materiale |
Thermoplastic Polyurethane with 13% Bio materiale |
Character | Hydrophilic Non-porous |
Hydrophilic Non-porous |
Standard Colors |
Transparent/White | Transparent/White |
Thickness [μ] |
15~25 | 20(±2) |
Width [mm] |
Max.2500 | 1,500 ±20 |
Weight [g] |
- | - |
Length/ Roll [m] |
15 micron : 1800 | 15 micron : 900 |
Minimum Order |
- | - |
Elongation [%] |
- | - |
✭Water proofness [mmH2O] *JIS 1092B |
>10,000 | >10,000 |
✭M.V.P [g/㎡・24hr] *JIS L 1099B-1 |
- | >60,000 |
✭M.V.P [g/㎡・24hr] *JIS L 1099A-1 |
>400 | >45,000 |
Certificate | TUV | TUV |
Remarks | 23% Bio material (Corn 100%) Without PE carrier |
13% Bio material (Corn 100%) With PE carrier |
※This is not the material spec but measuring data at factory for the comparison
VENSOZ®-TPU GRS LM, VENSOZ®-TPU GRS MM, VENSOZ®-TPU GRS HM
Keeps your body DRY & WARM

GRS TPU is made from post-consumer recycled raw materials.
- GRS (Global Recycling Standard) is an international recycling product standard and third-party certification. The goal is to increase the use of recycled materials in products and reduce/eliminate environmental hazards caused by their production.
- GRS TPU was made by remanufacturing recycled raw waste materials.
- It does not affect the physical performance and bonding, and the waterproofness can reach more than 10,000 (as seen on the graph).
- Successfully passed GRS Version 4.0 verification (IDFL Project NO.006601).
- TC certificate provided (additional charge).
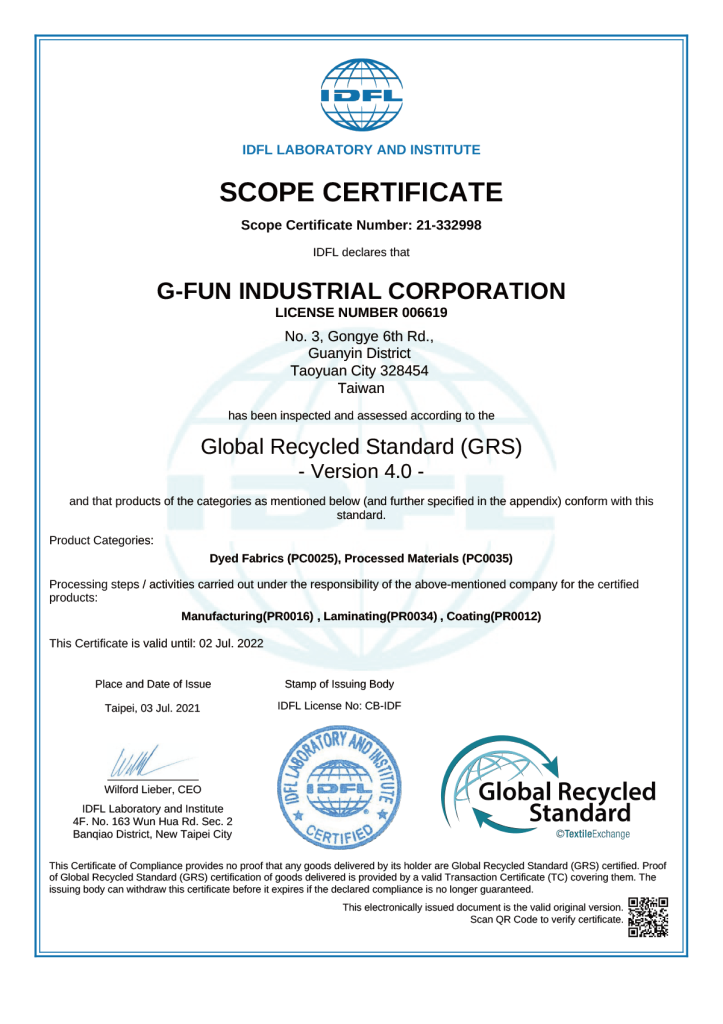
![]() |
![]() |
![]() |
![]() |
---|
Items | VENSOZ®-TPU GRS LM | VENSOZ®-TPU GRS MM | VENSOZ®-TPU GRS HM |
---|---|---|---|
Composition | Thermoplastic Polyurethane 100% |
Thermoplastic Polyurethane 100% |
Thermoplastic Polyurethane 100% |
Character | Hydrophilic Non-porous |
Hydrophilic Non-porous |
Hydrophilic Non-porous |
Standard Colors |
Transparent/White | Transparent/White | Transparent/White |
Thickness [μ] |
20(±2) | 20(±2) | 20(±2) |
Width [mm] |
Max.2500 | Max.1600 | Max.1600 |
Weight [g] |
- | - | - |
Length/ Roll [m] |
15 micron : 1800 | 15 micron : 900 | 15 micron : 900 |
Minimum Order |
- | - | - |
Elongation [%] |
- | - | - |
✭Water proofness [mmH2O] *JIS 1092B |
>10,000 | >10,000 | >10,000 |
✭M.V.P [g/㎡・24hr] *JIS L 1099B-1 |
- | >10,000 | >60,000 |
✭M.V.P [g/㎡・24hr] *JIS L 1099A-1 |
>400 | >4,000 | >4,500 |
Certificate | GRS TC certification | GRS TC certification | GRS TC certification |
Remarks | Without PE carrier. | With PE carrier. | With PE carrier. |
※This is not the material spec but measuring data at factory for the comparison
VENSOZ® - SF
Keeps your body DRY & WARM

DEVELOPED ST-PU PELLET BY OUR OWN ⇒
MAKING VENSOZ SF EXCLUSIVELY!
After years of hard work, our team has developed a solvent-free, non-fluorinated functional waterproof and breathable PU film, "VENSOZ® - SF," which addresses existing environmental concerns in the waterproof and breathable film market! Unlike conventional waterproof and breathable PU films that require solvents, "VENSOZ® - SF" is manufactured using a special process and proprietary functional materials developed in-house, eliminating the need for solvents altogether. This enables us to achieve the required functionality while avoiding excessive impact on the environment!
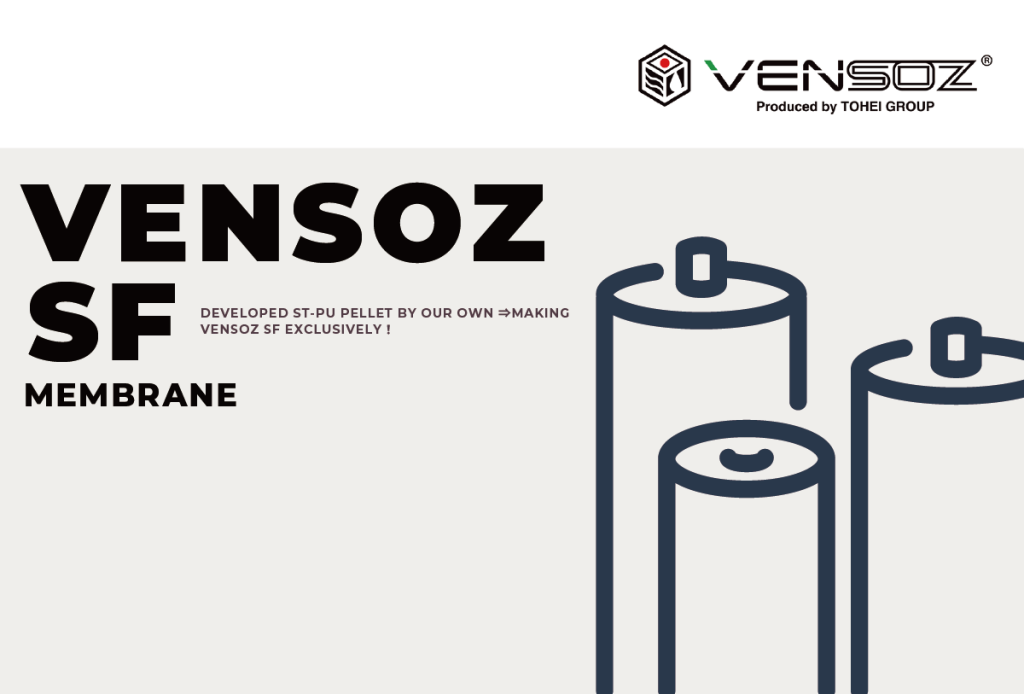
![]() |
![]() |
![]() |
![]() |
---|

After years of hard work, our team has developed a revolutionary solution that isa solvent-free, less CO2 emissions PU membrane!
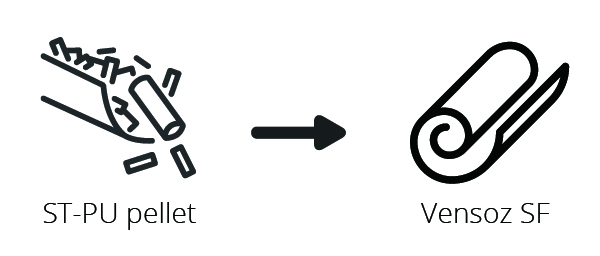
We have developed pellets called "ST-PU" that can be used in the same production process as TPU film, leveraging the knowledge of high-performance waterproof and breathable PU film resin from Japan and taking advantage of its superior physical properties.
Features:
- Compared to conventional waterproof and breathable films, both the raw materials and production are more environmentally friendly.
- Excellent heat resistance allows for processing with seam tapes similar to general PU films.
- Outstanding breathability and washability.
- Reasonable price.
- CO2 emissions are reduced by approximately 2/3 compared to conventional PU films.
- This is mainly due to the elimination of the long drying process during production.
Performance review |
|||||
---|---|---|---|---|---|
WP | MVP | RET | |||
JIS L 1092 | JIS L 1099 A1 | JIS L 1099 B1 | ASTM E96-1995 | ISO 11092 | |
Vensoz SF 15um |
over 16,000mm | 4,100 G/M2 24HRS |
55,640 G/M2 24HRS |
21,140G/M2 24HRS |
2.769 PA.M2/W |
Vensoz SF 18um |
over 16,000mm | 2,990 G/M2 24HRS |
62,020 G/M2 24HRS |
19,650G/M2 24HRS |
5.133PA.M2/W |
The data provided is not guaranteed; it represents the actual testing results from third-party inspections.
Market situation
CO2 EMISSIONS/PFAS/SOLVENT
The issue of carbon dioxide emissions is consistently one of the most critical concerns in the field of environmental protection. Our products achieve higher production efficiency by optimizing materials and manufacturing methods compared to conventional waterproof breathable films, thereby avoiding excessive energy consumption. Additionally, our products are free from environmentally harmful chemicals such as PFAS and solvents. Compared to solvent-based polyurethane films, our products reduce carbon dioxide emissions by approximately 75%. Compared to water-based polyurethane films, they reduce carbon dioxide emissions by approximately 80%. (Please note that this data is based on testing results from our laboratory and does not represent guaranteed values).
75% Less CO2 emission than Solvent-based PU MEMBRANE.
80% Less CO2 emission than Water-based PU MEMBRANE.
The data provided is not guaranteed; it represents the actual testing results from our lab.
CO2 Emissions ① While making PU resin | ||||
---|---|---|---|---|
No. | Item | Emissions CO2/KG | Resin solid content | After deduction CO2/KG |
AA | PU (Solvent-based) | 4.78 | 30% | 15.9 |
BB | PU (Water-based) | 7.65 | 30% | 25.5 |
CC | Vensoz SF pellet | 8 | 100% | 8✔ |
CO2 Emissions ② While making membrane | ||||
No. | Item | Emissions CO2/m | Resin solid content | After deduction CO2/m |
AA | PU (Solvent-based) | 0.884 | 30% | 2.94 |
BB | PU (Water-based) | 0.998 | 30% | 3.32 |
CC | Vensoz SF pellet | 0.1 | 100% | 0.1 ✔ |
Low heat resistance
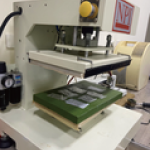
Typically, TPU has heat resistance up to about 90-120 degrees Celsius, but VENSOZ® - SF can withstand temperatures of approximately 140 degrees Celsius.
This allows VENSOZ® - SF to have an advantage over TPU in high-temperature processing, especially in applications such as seam tape and lamination, where the range of applications is significantly expanded.
Item | Thickness | 90 °C | 120 °C | 125 °C | 130 °C |
---|---|---|---|---|---|
✔ Vensoz SF (V1) | 18±2 | ○ | ○ | ○ | ○ |
TPU- (Made in Taiwan) |
18±2 | ○ | × | × | × |
Swelling issue
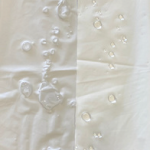
The importance of water repellency in the waterproof performance of functional textiles has shifted primarily from conventional fluorine types to fluorine-free types due to environmental concerns.
As a result of this processing change, the water repellency of fabrics has decreased significantly, leading to a pronounced swelling phenomenon in the moisture transfer mechanism of non-porous waterproof breathable films. Therefore, reducing the swelling value has become one of the important challenges for functional improvement.
Resin | Description | Moisture permeability performance [g/m² · 24hr] *JIS L 1099B-1 |
Swelling data |
---|---|---|---|
Vensoz SF | Item VENSOZ® - SF | 50,000 | 4% ✔ |
TPU | Normal high MVP type TPU | 50,000 | 14% |
PU | Solvent based polyurethane membranes | 100,000 | 16% |
Swelling tests involve immersing the test specimen in water and confirming the difference in elongation rate compared to before treatment. Please refer to the table below. The normal expansion rate of moisture-permeable TPU/PU is approximately 14% to 16%, while the expansion rate of VENSOZ® - SF has been significantly improved to about 4%.
The data provided is not guaranteed; it represents the actual testing results from our lab.
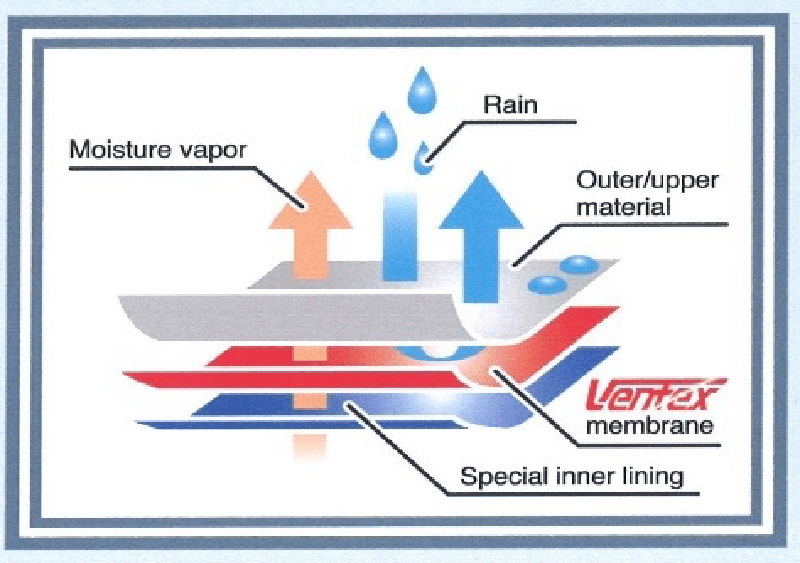
As mentioned earlier, by eliminating solvents in the manufacturing process, we have reduced carbon dioxide emissions and avoided the use of harmful raw materials such as fluorine.
The VENSOZ® - SF film comes in two thicknesses: L and H. The H variant offers excellent waterproofing, while the L variant provides excellent breathability, both maintaining excellent breathability and low swelling effects.
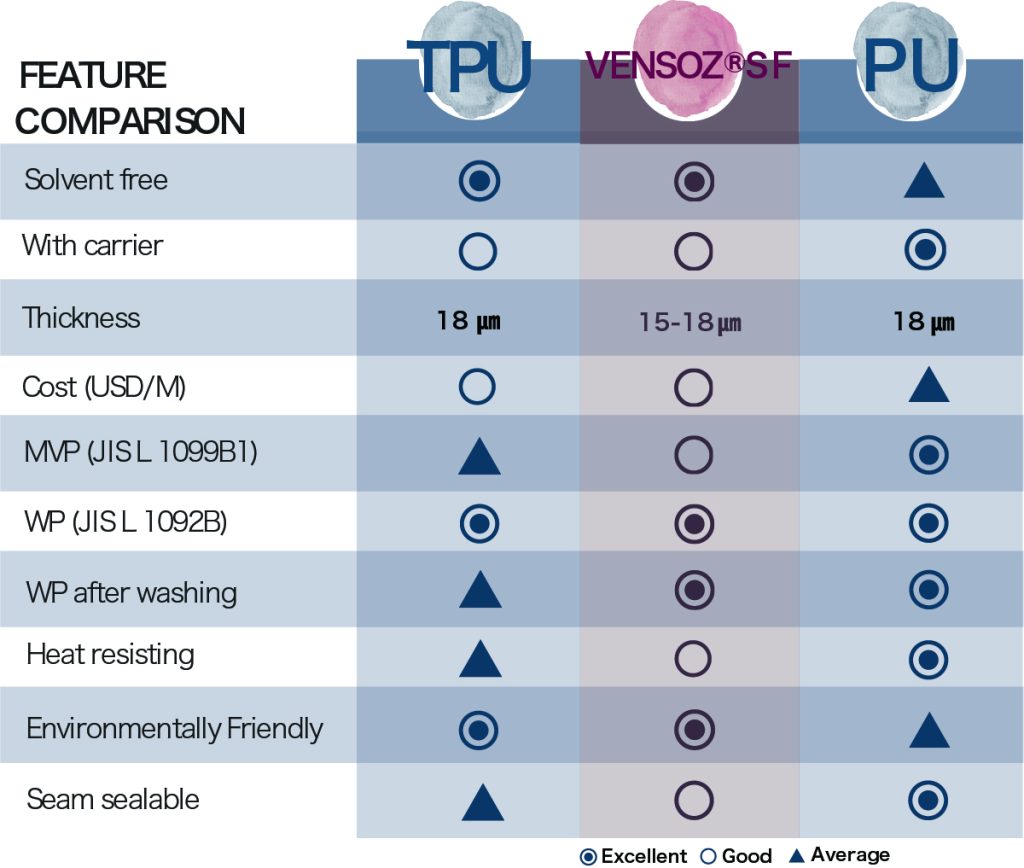
Of course, both specifications also have a waterproof pressure resistance exceeding 15k and are suitable for seam sealing at high temperatures.